一. 事故產生原因分析
(1)原料的不穩定性決定事故多。化工企業生產中很多化工原料的易燃性、反應性和毒性決定了易出現火災爆炸及中毒事故的情況。而壓力容器的爆炸及反應物的爆燃,都會產生破壞力極強的沖擊波。
(2)生產過程事故多。化工生產中的副反應、處于臨界狀態或爆炸極限附近的反應都易引發火災事故。
(3)設備破損引起爆炸泄漏。生產原料的腐蝕、生產壓力的波動、生產流程中的機械振動引起的設備疲勞性損壞以及高溫、深冷等導致的壓力容器破損;設備設計不合理或加工工藝存在缺陷,都易引起事故發生。
(4)小型化工企業的工人素質往往不高 , 職工對作業系統的操作事,隨意刪改安全操作規程 , 誤操作或在設備檢修時發生事故的幾率高。特別是在檢修工作時 , 焊接與切割、使用噴燈、電鉆、砂輪等可能產生火焰、火花和赤熱表面的臨時性作業往往都是在易燃易爆的化工裝置區域內進行。違章動火主要體現在: 違章指揮 , 動火審批不嚴; 貿然動火釀成火災; 現場監督、現場措施不力。
綜上所述,造成化工事故的根本原因主要在于人的過失,上述列舉的事故起因,無不與人相關,事故既然主要由人造成的,那么人們就必須想方設法的去控制事故的發生。
二.預防措施
(1)科學規劃,合理布局。要求對化工企業的選址進行嚴格規范。要充分考慮企業周圍環境條件、散發可燃氣蒸氣和可燃粉塵廠房的設置位置、風向、安全距離、水源情況等因素,盡可能設置在城市的郊區或城市的邊緣,從而減輕事故發生后的危害。
(2)嚴把建廠審核和設備選型關。化工企業的生產房應按國家有關規范要求和生產工藝進行設計,充分考慮防火分隔、通風、防泄漏、防爆等因素。同時設備的設計、選型、選材、布置及安裝均應符合國家規范和標準,根據不同工藝流程的特點,選用相應的防爆、耐高溫或低溫、耐腐蝕、滿足壓力要求的材質,采用先進技術進行制造和安裝,從而消除先天性火災隱患。
(3)加強生產設備的管理。一般講,經過一段時間的運行,受高溫、高壓、腐蝕影響,設備材料就會出現性能下降、焊接老化等情況,可能引發壓力容器及管道爆炸事故。此外還要做好生產裝置系統的安全評價。
(4)強化教育培訓,做好事故預案。化工企業從業人員要確保相對穩定,企業要嚴格職工的全員消防安全知識培訓、特殊崗位安全操作規程培訓并持證上崗、處置事故培訓等,要制定事故處置應急預案并進行演練,不斷提高職工業務素質水平和生產操作技能 ,提高職工事故狀態下的應變能力。
(5)落實安全生產責任制,杜絕責任事故。從領導到管理人員,明確并落實安全生產責任制,特別是強化各生產經營單位的安全生產主體責任,加大責任追究力度,對嚴重忽視安全生產的,不僅要追究事故直接責任人的責任,同時要追究有關負責人的領導責任,防止因為管理松懈,“三違”等造成事故。隨著化工安全生產職責的明確,責任的落實,管理環節嚴謹,基本可以杜絕責任事故的發生。
三.建議
化工企業部門應根據行業特點,制定化工企業重大事故應急救援方案編制的指導性導則,企業一句導則的只要內容以及本企業重大危險源的具體實際情況,編制重大事故應急措施方案,對企業職工進行實施應急措施培訓和教案,并進行模擬演練,按照應急措施反感進行救助和躲避,以提高企業領導和全體職工在發生重大事故后的應變能力。通過各種措施的落實,將事故造成的損失控制在最低限度。
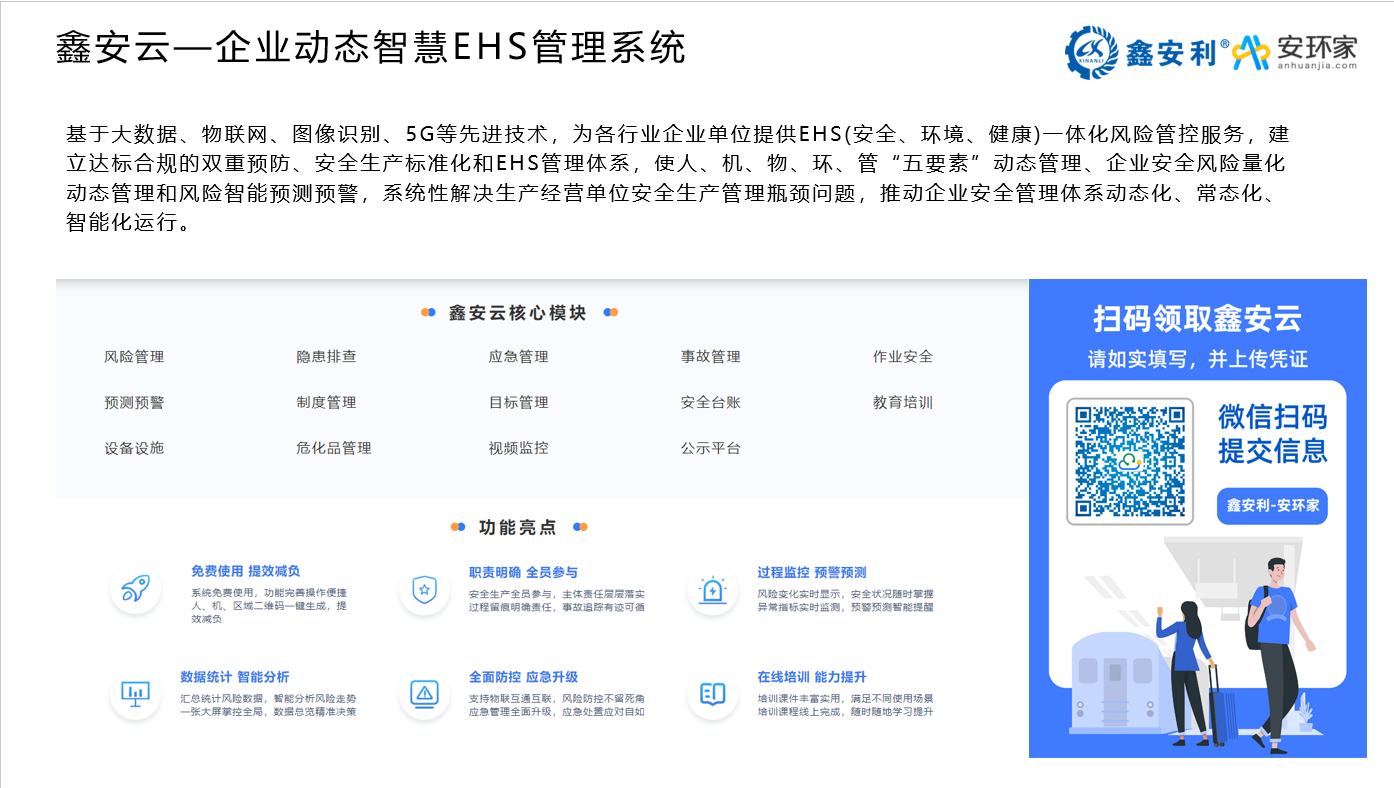